Industrial Dedusting Systems
Dust Extraction Systems – Dust Collectors
We execute dust extraction systems for different industries (e.g. power engineering, metallurgy, founding, as well as chemical, food, and woodworking industries). Depending on the customer’s requirements, we implement projects in the “turnkey” system (all project stages from the design through production and assembly of system elements, start-up and service) or in the scope indicated by the investor (e.g. design of a dust extraction system plus fabrication of an extraction unit). Due to our considerable experience in explosion safety solutions, we place special emphasis on systems for extracting flammable and explosive dusts, gases, liquid vapours and hybrid mixtures.
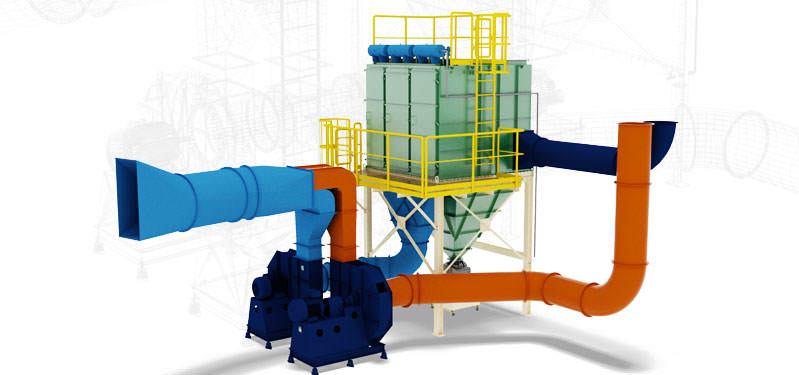

Contact our engineer
We will answer questions about: offer, technical specification, delivery, assembly.
Scope of works performed – dust extraction systems
- preparing concepts and designs for all works
- manufacturing dust extraction units and key elements of the system
- developing and implementing the control system
- assembly, start-up and service of the dust extraction system
- developing concepts and implementing safeguards limiting the risk and effects of an explosion
- working out an explosion risk assessment and/or an explosion protection document
Completed projects – examples
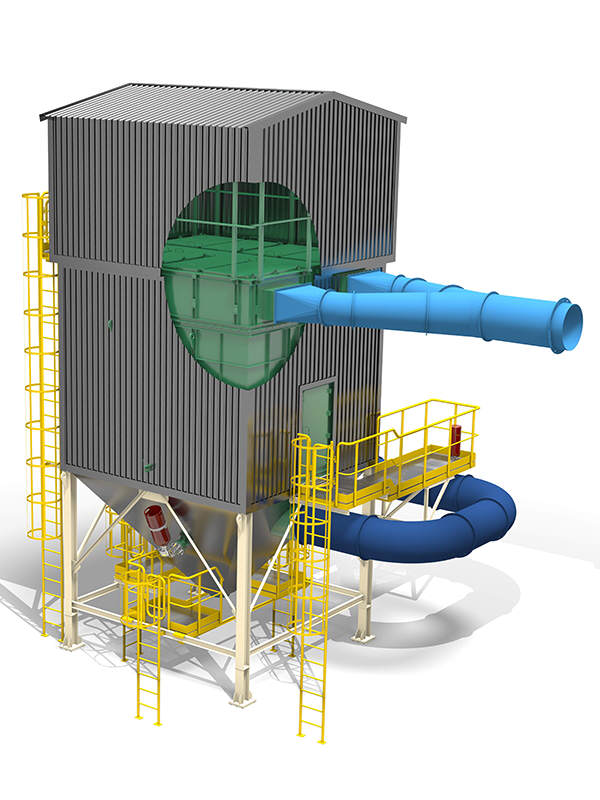
Coal dust filter protected against explosion effects by an explosion dumping system (HRD cylinder) and an explosion decoupling system (HRD cylinder) as delivered to a power plant belonging to Polski Koncern Energetyczny (Polish Energy Concern). The “turnkey” delivery included designs for all works, manufacturing the dedusting unit and pipelines, connecting the dust extraction system to the power plant Distributed Control System, preparing an as-built explosion risk assessment.
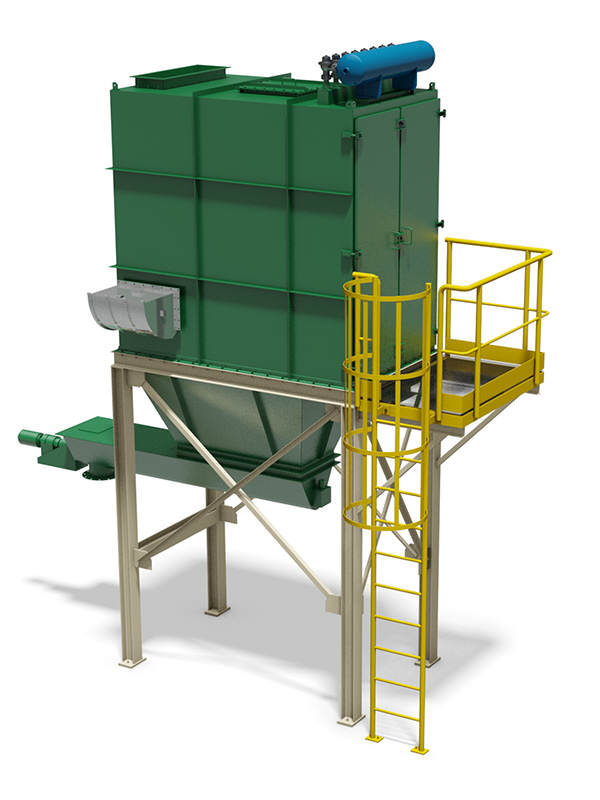
Dedusting unit designed and delivered in the “turnkey” system to the Stalprodukt company’s production plant. The system has been adjusted to explosion safety requirements (ATEX directives). The filtration unit has been protected against dust explosion effects by flameless explosion venting and explosion decoupling (non-return damper).
Dust extraction systems in explosion-proof design – ATEX
Due to our considerable experience in explosion safety solutions, we place special emphasis on systems for extracting flammable and explosive dusts, gases, liquid vapours and hybrid mixtures. In such cases, we apply both the preventive solutions that limit the risk of explosion as well as explosion-proof systems required by law (explosion damping, explosion relief, explosion decoupling).
Similarly to the works on design and execution of dust extraction systems, also aspects related to the system safety may be executed in the “turnkey” system or selectively, depending on the investor’s needs.
Note – explosion hazard
When flammable dusts, gases, vapours, or hybrid mixtures occur in the process, there is a serious risk of explosion. This phenomenon may lead to destruction of the dedusting unit, as well as of the whole plant (most frequently, it is caused by propagation of the explosion wave to the remaining part of the system, a secondary explosion or a fire resulting from the explosion). Pursuant to the Polish and European regulations, such type plants should be adequately protected against explosion effects.
Design works – dedusting systems
Design works – dedusting systems
The work on the task assigned begins with the development of the concept of the dust extraction plant. In the subsequent stages, we prepare construction designs, detail designs for respective works and a design of the filter unit. Our experience allows us to design installations with a capacity of up to 1.5 million cub. m of extracted air per hour.
The projects executed by us meet all explosive safety requirements.
Control and automation – dedusting systems
Our expertise allows us to provide control systems for process plants, especially for dust extraction and central vacuum installations. The solutions proposed are based on programmable logic controllers which make it possible to adjust flexibly system operating conditions to the customer’s requirements and the process.
In the cases of extraction of combustible and explosive dusts, vapours of liquids and gases, where the application of explosion proof systems is required, these systems are combined with the master control system.
Exemplary dust extraction plant control systems:
- dust extraction systems are operated as self-contained units not related to other systems,
- dust extraction systems work in tandem with supervisory control systems,
- dust extraction systems function as supervisory systems for dedusted plants.
Control systems may be equipped with alphanumeric displays for displaying operating data and with timers for selected devices. Remote control ON/OFF boxes with starting readiness signalization and operation signalization are applied for facilities with dispersed service lines.
The control system also monitors the system operating conditions and protects the system against being operated with admissible parameters overrun. The overrun of admissible parameters may be signalled to operators and in the absence of any reaction, the system will be switched off automatically.
Installation, start-up, service – dedusting systems
Thanks to our own service and installation departments, we provide efficiently the delivery of installation components to the construction site, the subsequent assembly and putting into operation. In the next stage, the plant is included into our warranty and post-warranty service system.
Our services include:
- explosion safety audits,
- developing concepts of protection of dust extraction systems against explosions,
- implementing preventive measures and explosion safeguards,
- working out explosion risk assessments and/or explosion protection documents.
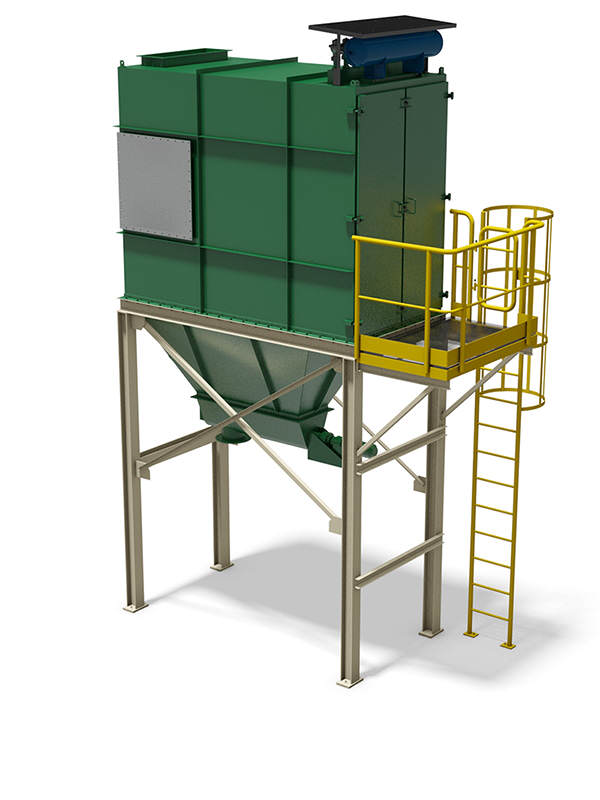
3d design of a dedusting unit protected against explosion effects by a relief system (decompression panel) and explosion decoupling (HRD bottle, not shown in the figure). The above filter is a core of the dust extraction system delivered “turnkey” to the Saint-Gobain company’s production plant.