Problem:
- A sealing machine was used for sealing packaging with flammable polyol content
- However, the high temperature of the machine’s jaws posed a fire risk
- Being the plant’s only machine of this kind, its downtime could cause major losses
- During negotiations with the insurer the plant’s management decided to have a dedicated extinguishing system installed
- However, the machine has to work 24 hours a day, which makes the installation difficult
Solution:
- According to our analysis, gas will not, unlike water, foam or dry powder, have a negative effect on the device
- We didn’t extinguish the whole machine but used local extinguishing zones instead, which enabled us to use the gas system, even though the machine case is not sealed (only side walls are integrated)
- Working closely with the Client, we planned the installation times precisely
Fire Hazard Posed by the Sealing Machine
Sealing machines often come with the two most important fire conducive properties: flammable substances and hot parts that can become a source of ignition. The same principle applied in this case.
The machine fills two-chamber bags with polyol and isocyanate, and then its hot jaws seal the bags. Polyol is, however, a highly flammable alcohol, and you are instructed in its safety data sheet to keep it away from heat, hot surfaces, sources of sparking, open flame and other sources of ignition. Then, these two factors combined make it all too easy for a fire to start.
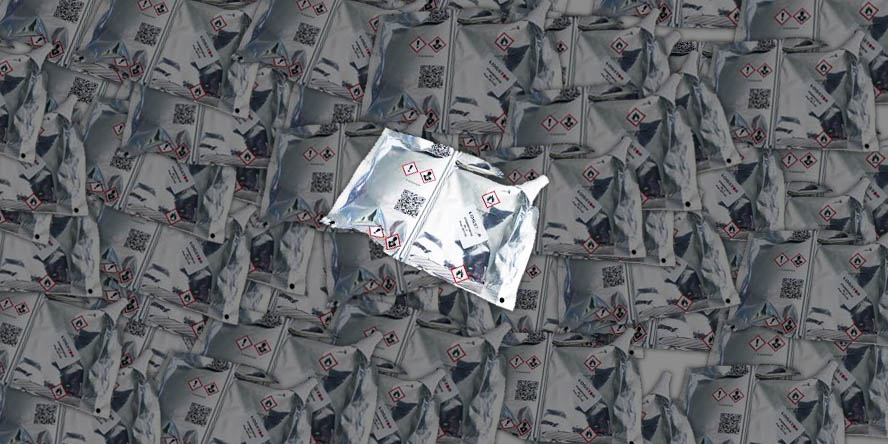
Photo 1: Machine with a fire protection system sealing a bag
It should be mentioned that the Client has been aware of the problem and made every effort to make the production process safe. Accordingly, the plant had already been equipped with a number of solutions and procedures that reduced the risk of fire. In addition, the building was fitted with an extensive fire suppression system.
Insurance Audit
The insurance audit is the basis for determining the rates that a manufacturing facility incurs. In extreme cases, an insurer will be likely to reject the contract if the level of risk is too high. No such risk occurred in our case.
However, it was agreed during the multilateral talks that the sealing machine is crucial for production continuity. Not only could a fire result in material damage, but also in high costs due to factory downtime. In an extreme case, the fire could spread to the building threatening the remaining infrastructure and, above all, the workers.
As a result of talks with the insurer, the factory management decided to have a dedicated fire extinguishing system installed to protect the machine against fire. The solution was a win-win for both parties.
How to Extinguish a Fire in Manufacturing Machinery
In most cases, gaseous fire suppression is the best method of protecting manufacturing machines, including welding machines or CNC machine tools. While wet agents could damage them, which should be prevented, using dry chemicals would require the cumbersome cleaning and lengthy downtime of the machine. Gases, on the other hand, do not adversely affect the protected device in any way. This means that restarting operation after a fire extinguishing system has been triggered takes much less time, which reduces the downtime losses.
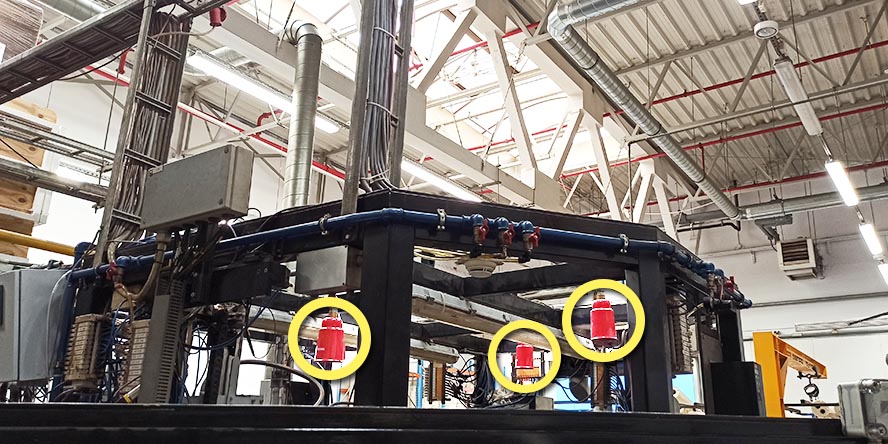
Photo 2: Machine with a fire protection system sealing a bag
Gaseous fire suppression is the most common method of extinguishing machinery fires. “However, we analyse each case separately”, says Mateusz Świtała, who is in charge of the fire protection department in the WOLFF GROUP. “For example, our task in another project was to provide protection for a machine that sealed tea bags – the same as those you brew every day at home. In that case, a spark detection and extinguishing system proved to be the optimal solution.
But back to the method of protecting the machine that fills and seals packaging. Having analysed the problem, we found several points where ignition was possible in the machine. Furthermore, we were able to specify their exact location. With this in mind, we decided to use a precise extinguishing system, which will deal mainly with those sensitive areas. In other words, we didn’t extinguish the whole machine, but we focused primarily on the really hazardous areas instead.
Optical smoke and temperature detectors are responsible for automatic fire detection and signalling. The extinguishing agent is released manually by means of local release stations located around the machine fencing and at the packing station.
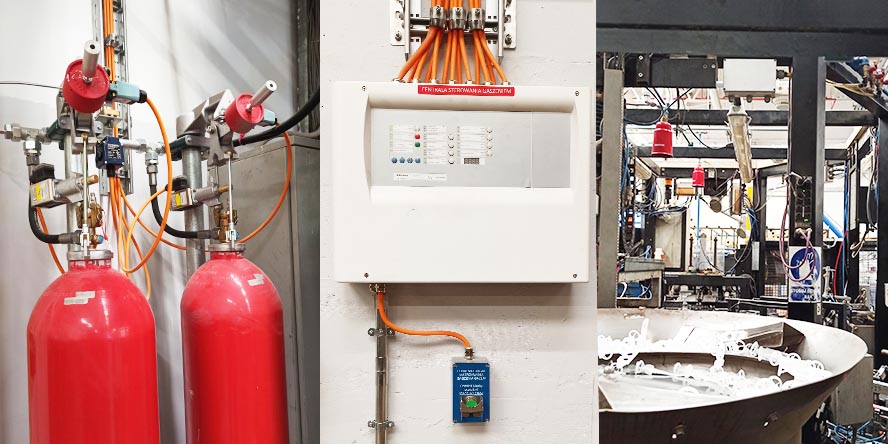
Photo 3: Gaseous fire suppression of a sealing machine in selected CO2 feed locations
CO2 As an Extinguishing Agent
Carbon dioxide can extinguish fire by reducing the airborne oxygen concentration of the protected area from 21% vol. to the level of 15% vol. and below. Supporting the extinguishing process is rapid cooling which takes place during the expansion of carbon dioxide accumulated in the cylinders under the pressure of 52 bar at the temperature of 15ºC. The use of a fire suppression system is to extinguish a fire in the initial phase, after reaching proper extinguishing concentration in a required time.
Do Not Interfere, in the First Place
Our Client’s primary requirement was to interfere in the production process as little as possible. In simple terms, we were not to interfere or hinder production. The task was made all the more difficult by the fact that the work had to be carried out on the machine that operated 24 hours a day.
Thanks to a very close collaboration with the Client, every day we would prepare a schedule of installation works. First of all, it took the plant production needs into account, which ensured that no downtime or related possible costs occurred.