When we start writing other articles for our website, describing individual implementations of the WOLFF GROUP in the field of explosion and fire safety in the industry, we often begin with a short summary of the problem faced by our client at their industrial site, and about the solution we have delivered. The genesis of this article, however, is quite different…
You have probably stumbled upon at least one of the quotes from Bartosz Wolff – the CEO of the WOLFF GROUP here and there on our website:
Things do not always go smoothly. However, we never left any of our partners in need. We have always pursued the goal TOGETHER.
We do not want to be another anonymous company founded on superficial, fast-food-like, relationships. We are looking for more in business – trust, partnership and a human face. These are the foundations, on which we want to build the WOLFF GROUP. This is not easy in a world dominated by the corporate, cold business style. However, I can assure you that we will follow our own way. The way of business with a human touch.
It is through this reference to the words by Bartosz Wolff that we want to show how long-term cooperation with the WOLFF GROUP in the field of explosion and fire safety may look like. We will use the example of one of the larger Capital Groups on the Polish energy and heating market.
Fire protection for key installations
When we started our cooperation with the investor, almost all the facilities and buildings required minor or major upgrades in terms of fire and explosion safety. It was therefore clear to both us and the managers in the described Capital Group that it was impossible to implement all the investments simultaneously. It was not only about the total budget for all the works required by the fire safety expert and by the insurer, but also about the fact that the site could not afford production downtimes, as it delivers hot water to thousands of households in the district heating network of one of the largest cities in Poland.

A part of the control system of the inclined bridge sprinkler system
In view of this fact, the investor divided the necessary upgrades into a number of phases to be carried out over a period of several years. The four stages outlined below can be categorised as of key importance to the fire safety of the entire site. We have implemented these stages over the last 5 years: starting from the sprinkler protection of the inclined bridge implemented in 2018 and ending with the upgrade of the fire-fighting pump station and the fire-fighting water tank released for use in the third quarter of 2022.
During these 5 years, the investor knowing it has an obsolete pump station, also ordered the implementation and delivery of an emergency supply for the fire-fighting system using a separate Diesel-powered pump, such that it ensured continued fire protection while waiting for the works related to the comprehensive upgrade of the pump station to begin.

Sprinkler protection for the inclined bridge
- We divided the 200 m long inclined bridge into 12 sprinkler sections.
- We installed two sub-stations with 12 sprinkler sections and provided them with water supply.
- We protected pipes which could potentially freeze with an adapted pipeline heating system.
- We ensured that the installation complied with the FM Global guidelines. All components had the CNBOP approvals.
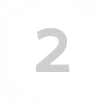
Fire signalling system for the inclined bridge
- We developed a comprehensive concept, which had to take into account the extremely difficult working conditions resulting in the risk of losses potentially caused by false alarms.
- We used two independent lines of linear temperature detectors (sensor cables) resistant to interference from extremely harsh environments.
- We have ensured the ability to quickly detect a fire at the smouldering stage. We have thus limited the potential losses.
- We supplied various types of optical and acoustic signalling devices, such that all employees could be immediately informed of the danger, regardless of the difficult working conditions at the facilities of the investor.
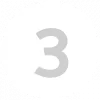
Upgrade of the internal hydrant system
- Installation of an internal hydrant system connecting 11 fire risers
- Installation of emergency supply stations for the main fire risers
- Execution of works at an operating facility and in difficult working conditions: high temperature and high levels of dust.
- We increased the pressure in the system by more than 1 bar and ensured the required capacity.

Fire-fighting water tank and pumping station.
- Comprehensive fire-fighting pumping station upgrade: from the design, through delivery and assembly to the E/I&C and electrical installation works, down to the finishing works and creating documentation.
- Two fire-fighting pumps and two jockey-type pumps for washing water
- Water tank with a capacity of up to 900 m3 for fire-fighting purposes
Further fire safety projects
The aforementioned realisations were not the only projects we carried out at the fire protection facilities of the investor during the five years of cooperation. The management of the combined power plant gradually improved the fire safety of the individual parts of their site. We have worked on a number of other tasks, noteworthy of which included sprinkler system protection for oil tanks and the transformer, as well as smoke extraction system implemented in stairwells and an upgrade of basic, emergency and evacuation lighting therein.
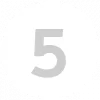
The oil tank sprinkler system
- Purpose: surface cooling enabling quick containment of fire when the fire-fighting action begins.
- The first oil tank is protected by two levels of sprinklers at of 0.00 m and +5.30 m.
- The second tank is protected by three rows of sprinklers with four nozzles in each, suspended from the ceiling.
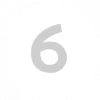
A sprinkler system intended for transformer extinguishing
- We designed a sprinkler system protecting the transformer. Water flow in the system is activated manually when a fire is detected. All the sprinklers of the particular sprinkler section (group) will then activate.
- The connection of pipeline elements around the transformer was implemented using quick connections, such that a part of the ring may be removed if necessary and access to the equipment is possible.
- We expanded the sprinkler sub-station with a flooding station (actuating valve), including a cut-off bolt valve located under the station.
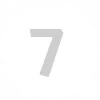
Smoke extraction system in stairwells
- As part of a project to adapt the combined power plant buildings to fire safety requirements, we installed a smoke extraction system in the stairwells.
- We supplied smoke dampers with an electric smoke control system, opening to an angle of at least 140o
- We connected the dampers to the extinguishing control panel.

Upgrade of basic, emergency and evacuation lighting
- We carried out an upgrade of the primary, emergency and evacuation lighting in the stairwells of two blocks of the combined power plant.
- We carried out calculations for the existing lighting, including a visualisation of the anomalies which had to be corrected.
- In addition to the fixtures, we installed lighting panels, lighting switches, junction boxes and electric shock protection installations.

Sprinkler over an inclined bridge
ATEX: Explosion safety projects
The combined power plant fires both coal and biomass. The dust from these products, which are the sources of energy needed to generate the system heat, is explosive. The investor was therefore obliged to comply with the requirements of the ATEX directive and to protect the installation.
The ATEX Directive, introduced into the Polish legislature by the relevant Regulations, requires the employer to take the following actions, in turn:
- elimination of explosive atmosphere formation,
- elimination of the possible ignition source for explosive atmospheres,
- providing installation protection from the effects of an explosion, i.e. reducing the explosion risk and its consequences to an acceptable level.
In the case of closed or enclosed installations or components such as ducts, pipelines, bucket-type elevators and dust extraction systems, systems minimising the effects of an explosion can be used effectively. This was the case with biomass firing installations, where we were able to propose explosion suppression and isolation systems. We started working with the investor in this field as early as 2012, during the time of a real “biomass boom” in the energy sector in Poland.
On the contrary, in the case of the huge and open coal conveyors in carbonisation galleries, it is physically impossible to use advanced explosion-proof systems. In this case, the focus remains on explosion prevention. It involves the elimination of areas where ignition can occur. Practice shows that ignition can occur within a huge volume of transported material, and it can also be the result of faulty equipment or equipment unsuitable for use in explosive atmospheres.
The ignition of material transported on large conveyors can only be eliminated through the use of conveyor detection and extinguishing systems – our work in this area is described in sections 1 and 2 above. As far as the machines and equipment involved in the material transport are concerned, we had to focus on the improvement of their reliability and their adaptation to the ATEX requirements – as described below, in section 9. On the other hand, the last section is related to the aforementioned biomass installation protection, where our work started in 2012.

Upgrade of equipment and of the electrical installation at the carbonisation facilities – adaptation to the requirements of the ATEX directive
- We replaced the previously used equipment, devices and installations with their counterparts with the relevant EX and IP-5x certificates.
- The drive upgrades included replacement of the drive motors together with the reducers and drive drums. In the case of the two conveyors, the drives were provided as gear motors. In the case of the remaining drives, we offered drive unit sets: an induction motor – a helical bevel gear. The solutions used guaranteed fault-free operation of the conveyors in winter conditions occurring in our country.
- We installed new cable switches along the route of the belt conveyors.
- We used vibration sensors for coal level control inside the coppers. We used two sensor lengths, depending on their installation location. We also protected the sensors with suitable protective canopies.
- We have replaced the belt movement sensors for the upgraded conveyors with ones with the relevant ATEX Ex II 1D T100°C feature.
- We dismantled the old and supplied new optical and acoustic signalling devices.
- Local control boxes for the conveyors were also replaced. We made the boxes from polycarbonate (PC), of the SOLID type. They were provided with buttons, the layout and functions of which we reproduced analogously to those available in the disassembled sets.
- We have provided new junction and connection boxes with the relevant EX features, installed along the process line of the conveyors. Outside the designated explosion hazard areas, we have also replaced the junction and connection boxes, as well as the water drainage pumps, gantry connectors, PV sprinkler cabinets, the cross-cable box for the water system and switchgears provided for internal needs. We have also replaced the wiring for all the new electric equipment.
- We have upgraded the primary and emergency lighting systems. When it comes to the primary lighting, we have replaced the existing lighting fixtures operating in the explosion hazard areas with their Ex counterparts (adequate for the hazard area). Outside the Ex zones, we have replaced the fixtures to provide improved IP protection.
- The emergency lighting upgrade was also designed with the adaptation of equipment to the ATEX requirements in mind, if a device operated within the explosion hazard area or the minimum IP rating, if the device operated outside the explosion hazard area.
- We carried out the functional tests of the replaced equipment at the carbonisation facilities, for conveyor line belts, as well as prepared the as-built documentation, measurement and quality documentation for the electrical and mechanical disciplines.
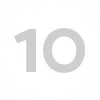
Ensuring ATEX safety at the biomass storage and feeding facility
- The history of our cooperation with the investor at the biomass storage and feeding facility dates back to 2012.
- Our work initially included the installation of explosion isolation systems on the filters and explosion suppression systems at the pellet elevator.
It should be noted here that the investor additionally protected the biomass silo with decompression panels – this part of the project proceeded without our involvement. After some time, the investor built new equipment in the direct vicinity of the silo. It turned out that a possible explosion inside the silo would have caused the ruptured decompression panels to release a fireball and pressure waves directly onto this new device. The investor asked us to solve the problem. We had to make changes such that the panel openings were used. We therefore decided to propose a flameless blast relief system. - The next step of the cooperation involved protection of the second bucket type conveyor for chips using an explosion suppression system.

The provided visual signalling system as one of the elements of the upgrade of 12 conveyors intended for operation in Ex areas
Trust, partnership, with a human touch
In the context of the cooperation with the described Capital Group, we asked Bartosz Wolff – the CEO of the WOLFF GROUP – about issues related to his past statements concerning the foundations of running a business and cooperation with customers. Here is what we heard from him:
“If we are to talk about the values and foundations of our cooperation with the clients, or with this particular client, we should refer to another statement of mine, which can be found on our website, under the ‘careers’ tab. The point is that there are no perfect companies – and we are not such a utopian company either. Processing this almost trivial fact within can change the perspective of the relationship between the business partners. It opens the eyes and ears to the needs of others, it allows you to listen to the other side, in other words, it is the foundation on which you can build such humane, partner relationships, and not a fast-food-like business as I have once put it.
To be a little bit more specific, the story of securing a biomass silo is probably the best example I could provide here. Originally, the investor did not install the decompression panels with our involvement, nor did it consult us about the impact of the used decompression system on the newly built unit. By the time the equipment was ready, it was, colloquially speaking, all said and done.
Could we have done something better as the WOLFF GROUP up to this point? In retrospect, I can say that yes, of course we could. Seeing the existing security features in the form of panels, we could have made sure that our partner knew all the advantages and disadvantages of the solution they used. First and foremost, the partner was aware it was not allowed to build new installations potentially exposed to hazard at the time of an explosion and panels bursting. Since then, we have always attempted to reach out with an additional initiative and expand the knowledge of our client in the fields of fire protection and ATEX.
Returning to our project, however… it was obvious we did not leave our partner in need. We had to recommend a different explosion protection system, which would mitigate the consequences of an explosion into the protected silo on the one hand, and on the other, use the openings after decompression panels present in the silo. We proposed the use of flameless explosion relief systems. We executed the assembly at the level of 35 metres, and thus the works required us to use specialised equipment and rope access. And although the dimensions of the new components were selected precisely – literally down to ‘millimetres’ – the proper preparation for assembly allowed us to complete it in one day.“