Problem:
- Maltodextrin, whey and milk powder pose a risk of explosion and fire.
- These products go to three dust collectors – the devices where, according to statistics, explosions occur most frequently.
- Aware of the risk, the project owner proposed to protect the system with panels with decompression ducts; although this solution is often the cheapest, in some cases it can generate high hidden costs.
Remedy:
- We performed selection calculations for four different types of explosion protection, including those proposed by the client.
- We demonstrated that the use of panels with decompression ducts would require costly works that the project owner had not considered.
- As a result, we proposed two alternative explosion protection systems that the project owner considered and selected an explosion suppression system.
Analysis of not fewer than 4 different solutions
Protection against a wrong decision
Implementation of protection system
Sugar Strengthens
In communist Poland, they said that ‘sugar strengthens’. And although the slogan was part of the propaganda of the time, Melchior Wańkowicz, the slogan’s author, was certainly right about one thing: there is tremendous power in sugar. It is a real bomb when in the form of airborne dust. Sadly, Imperial Sugar Refinery had this very tough experience – as an explosion at one of its plants led to a real disaster..
Sugar, however, is only an example. There are many more equally explosive dusts in the food industry. Read the story of our client who decided to bring a new section of the plant into compliance with explosion safety requirements.
Are these dusts explosive?
After this ‘soft’ introduction, which was just to intrigue you, dear reader, I will immediately hit the high spots, which is what technical people like best.
The story begins when a food industry plant decided to expand its production facility with three dust collectors. The equipment was to provide reception of bulk semi-finished products from the pneumatic conveying system.
The dust collectors received three different products, which all had one common denominator: they all posed a risk of explosion, as evidenced by the explosiveness parameters below. In addition, the end of the table shows sugar parameters for comparison, the product that caused the aforementioned tragedy at Imperial Sugar Refinery.
Products with explosive dust contents | Pmax (bar) | Kst (m*bar/s) |
Whey | 7,4 | 53 |
Skimmed milk powder | 7,8 | 109 |
Maltodextrin | 8,6 | 133 |
Sugar | 9,0 | 123 |
The figures don’t tell me anything, or how to interpret explosiveness parameters
These figures may not be clear to everyone, so we will try to explain how to interpret them.
Pmax specifies the maximum pressure that a given dust explosion can reach. In this case, it oscillates around 8 bar. Is that much? To answer this question, let us compare this value with the structural strength of equipment commonly used in industry. These include silos, intermediate tanks, dryers, dust collectors or bucket elevators: 90% of them have a strength of 0.2 – 1.0 bar.
However, let us return to the dust collectors in question. They had a design strength of 0.4 bar, which is as much as 20 times less than the maximum explosion pressure of the dust collected inside. What does this mean in practice? In one of our free on-line workshops, we analyse an actual explosion that destroyed three dust collectors and a building in 2.3 seconds.
Kst, or the rate of pressure rise over time describes the dynamics of the explosion. This is an extremely important parameter from the point of view of explosion protection system design. For the plant user, however, it is of secondary importance. Why? Figuratively speaking, Kst defines whether an explosion will develop to maximum pressure in half, one or two blinks of an eye. While this makes a huge difference to the explosion protection system, it is virtually irrelevant to humans. During this time, we are unable to escape, turn on the fire system or respond in any other way.
Let’s recap:
- We have three identical dust collectors.
- The design strength of each is 0.4 bar.
- The maximum dust explosion pressure in the dust collectors is between 7.4 and 8.6 bar.
- The rate of blast pressure rise is between 53 – 133 m*bar/sec.
- We have dimensioned drawings of dust collectors at our disposal.
How to protect dust collectors from explosion?
The industry is familiar with several anti-explosion techniques. Each has its advantages, but also has some limitations. The art of selecting the optimum explosion protection system is to consider each of the three key aspects:
- Compliance of the system with legal requirements,
- System impact on the production process,
- Costs of purchasing and servicing the explosion protection system.
For this project, we have progressed from simple explosion protection such as decompression panels, to flameless explosion relief, to explosion suppression. The selection of safeguards here was a process involving both the project owner, the contractor company that was to carry out the extension of the existing plant with the dust collectors in question, and us.
PROPOSAL 1: a decompression panel with a vertical duct
Firstly, we were asked to protect the dust collectors by means of a decompression panel with a duct that carries the effects of the explosion through the roof of the building to the surrounding area. The duct was necessary in this case because the law prohibits the use of decompression panels in spaces where people may be present, particularly in confined spaces.
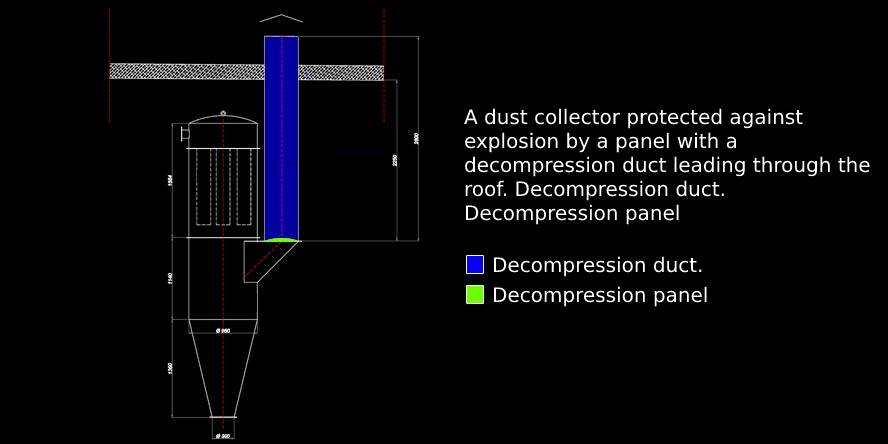
This solution is relatively cheap, but not without its drawbacks. In this case, the use of a duct would increase the required structural strength of the protected device. This is because the decompression duct causes an increase in the reduced explosion pressure Pred, i.e. the pressure to which the explosion pressure is reduced as a result of the tripping of the safety devices.
In other words, the same panel with a decompression duct has less efficiency than if it did not have this duct. This is mainly due to the fact that the duct causes an increase in flow resistance. In turn, the harder it is to get the blast pressure out of the instrument, the higher it will rise inside it.
The calculations we made showed that in this case the resistance of the dust collectors would have to be raised from 0.4 to at least 1.0 bar. Of course, this is feasible, but involves additional costs.
The physical installation of the dust collector reinforcements is a significant cost, but not the only cost that the decompression duct would generate. This also has to take into account the costs of complex strength calculations, breaking through a ceiling or a building wall, as well as the costs associated with designating a zone within the duct outlet where people, other equipment or buildings are not allowed to stay. All of this represents a hidden cost, so to speak, which the project owner has not yet taken into account.
PROPOSAL 2: a decompression panel with a horizontal duct
The effect of the decompression duct on increasing the strength of the protected instrument depends, among other things, on its length and the number of elbows. In a second step, we carried out calculations for a duct leading out not through the roof but through a wall.
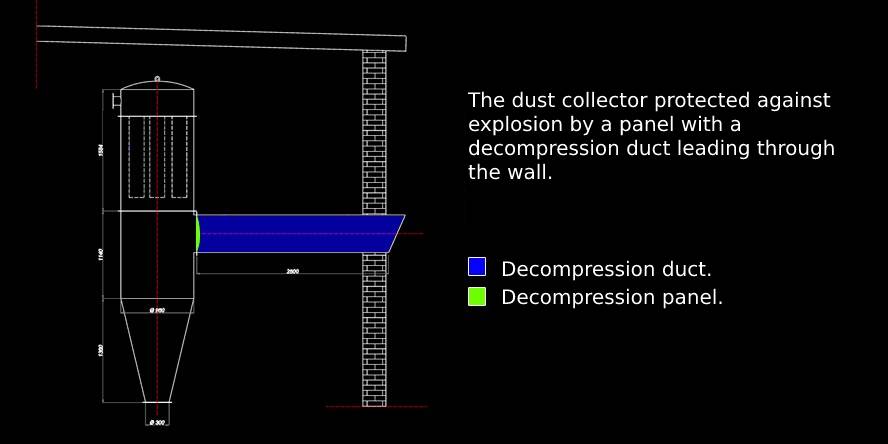
In this way, we got rid of one elbow and shortened the length of the duct slightly. This reduced the required structural resistance from 1.0 bar to 0.8 bar.
Once again, however, the costs involved in making the dust collector reinforcements, the duct itself and the wall opening were found to be so high that it is worth verifying how more advanced types of protection would compare.
PROPOSAL 3: flameless explosion vent
Our next step involved the verification of feasibility of using the so-called flameless explosion relief of the EVN valve type.
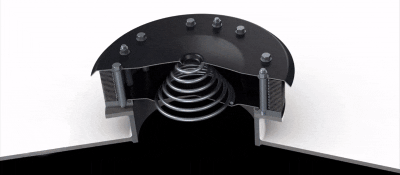
This type of protection takes the form of a valve that opens at the moment of explosion and releases the excess pressure into the environment. More importantly, the valve has a special type of heat exchanger that cools the escaping gases and extinguishes the fire. In this way, only residual pressure and gases cooled to a safe level get outside. All this means that this type of protection can be used indoors provided that:
- the volume of the room in question is at least 15 times the volume of the appliance to be protected,
- we establish a zone around the valve where people are not allowed to enter (1.5 m in front and 2 m around)

This solution has been used repeatedly to protect dust collectors without causing any problems. Nevertheless, the project owner was concerned that periodic blow cleaning of the filter elements with compressed air could cause the valve to open.
SOLUTION 4: explosion suppression
As the fourth solution, we proposed an explosion suppression system consisting of special detectors and extremely fast explosion suppression cylinders. This solution is the only one mentioned that does not allow an explosion to develop, extinguishing it at a very early stage.
This has the great advantage of not allowing a fire in the unit, which is typically the case with decompression panels in particular (EVN valves automatically close after an explosion which restricts air access reducing, but not eliminating, the risk of fire). In other words, explosion suppression guarantees the highest level of safety for both personnel and protected equipment.
Below you can see what a device protected by decompression panels looks like after an explosion followed by a fire inside.

What type of explosion protection has been selected?
We presented both the project owner and the plant extension contractor with 4 possible scenarios – 4 available explosion-proof techniques. We have shown their advantages, but also their limitations. We made a number of calculations. All this allowed the project owner to make the best decision from its perspective. In this case, an explosion suppression system based on a control central unit, sensors and HRD (High Rate Discharge) cylinders proved to be the optimal solution.
The operation principle of this safety feature is shown in the video below.
GENERAL NOTE – Explosion isolation
None of the above-mentioned systems will be fully effective if the protected system is not equipped with so-called explosion isolation. Its purpose is to immediately isolate the device in which the explosion occurred from the rest of the system. This prevents the explosion from penetrating into neighbouring instruments, which could lead to so-called secondary explosions. This is extremely important because this type of explosion is characterised by higher maximum pressure and dynamics. This means that even if the device in which the secondary explosion has occurred has one of the explosion protection systems mentioned above, it will in all probability not be effective.
At this point, we will once again refer to the explosion, which we analyse in detail during our free on-line workshop. This case perfectly demonstrates the consequences of the lack of isolation that led to secondary explosions. Immediately after this explosion, the plant authorities estimated the losses at PLN 5 million.
Competition – price is not equal
At one stage of the project, a competitor implementing explosion protection joined the discussions. All we knew was that their offer was significantly cheaper than ours. We were curious as to why there was such a big difference in price. Vigilance at this point was also shown by the project owner, who also wanted to discern what the reason for such a large discrepancy was. As it later turned out, the difference was due to a different approach to estimate service costs. We presented a price for servicing the entire system, which is key information for the project owner, while the competitor’s bid showed prices for servicing individual system components. The price quoted in the bid should therefore have been multiplied by the number of components.
To clarify: any explosion suppression system requires periodic maintenance. In our case, it has to be performed once a year, which is the longest period of time allowed by law (Reg. of Min. of Internal Affairs and Admin. of 2010.06.07 Journal of Laws 109, item 719, Section 3(3)). But that’s not all.
We address these types of considerations for comparing the prices of different security providers in one of our free guides. Refer to the document “How to convince the management to improve explosive safety”. It introduces an objective measure of cost called Total Cost of Ownership. It is a measure that has been introduced to the wider business by the international research and consulting firm Gartner. In the aforementioned document, we show how the Total Cost of Ownership can be easily applied to compare offers from different suppliers.