Problem:
- the furnace supplying hot air to the sawdust dryer generates sparks and hot particles which, through a pneumatic transport system, may enter the dust cyclone and the silo, which can lead to fire or explosion
- too short a distance between the drying drum and the cyclone prevents maintaining the required distance between the spark sensor and the extinguishing nozzle
- location of the drying installation and sawdust storage under an unheated station roof, which could cause the extinguishing water to freeze
Solution:
- protection of the duct between the drying drum and the dust cyclone and the transport line to the silo through a spark detection and suppression system
- extension of the duct between the dryer and the cyclone to ensure a minimum distance between the spark sensor and the extinguishing nozzle
- use of a heating system on the water installation exposed to negative ambient temperatures
Check the details of the implemented equipment and services:
Hazards during pellet production – examples
7 persons were injured in the explosion at the Georgia-Pacific plywood sheets production plant. Two of them – fatally. As indicated: “Despite the risks of explosion and deflagration with the presence of highly combustible dust and sparks, the dust collection system including the spark detection and suppression system, failed to meet numerous industry standards set by the National Fire Protection Association and FM Global.” After the incident, the court demanded from three companies a total amount of compensation of about PLN 134 million. The companies obliged to pay compensation are:
- manufacturer of the dust extraction installation (51% of the amount),
- manufacturer of the spark detection and suppression system (26% of the amount),
- Georgia-Pacific – the production plant where the explosion occurred (23% of the amount).
A fire of a sawdust silo located inside the production bay occurred at a wood processing plant in 2014. Fortunately, the situation was contained, and the fire did not move to the other bays. Unofficial sources reported that sparks from the fan contributed to the ignition.
Three years later (2017), a similar event occurred at a wood processing plant. Ignition and explosion occurred in the sawdust storage silo damaging the upper part of the silo. The probable cause of the fire was the introduction of impurities (metal chips from the production line) into sawdust. After the fire, losses were estimated at about PLN 50 thousand. Fortunately, no one was injured in the incident.
These are just three examples of the many that occur in the wood industry. In most of the technological processes associated with wood processing, sparks or hot particles are generated and can enter the filters, among others. They are one of the most common initiators of dust ignition and can cause a fire or explosion in pipelines, cyclone, and most frequently – in a silo.
Sawdust receiving, drying and storage plant
The plant in question consists of a hopper, a system for transporting wet sawdust to a drum dryer together with an oven supplying it with hot air, a dust extraction cyclone and a silo. Dry sawdust is collected from the drum dryer and then transported pneumatically to the cyclone where dust is extracted. From the cyclone, the sawdust is transported to the storage silo, also using pneumatic transport.
Experience shows that sparks and hot particles that can lead to fire or explosion are often generated in such installations. They may be of different origins. In the case of the described plant, they can be generated by an oven used to supply hot air to the dryer. Sparks can also be generated by impact e.g. a metal element against the inner walls of an installation. Such an element can enter the installation with sawdust – through the hopper.
It has therefore become necessary to effectively eliminate these threats. Spark detection and suppression systems are most commonly used in such cases and such a solution was also applied for this plant.
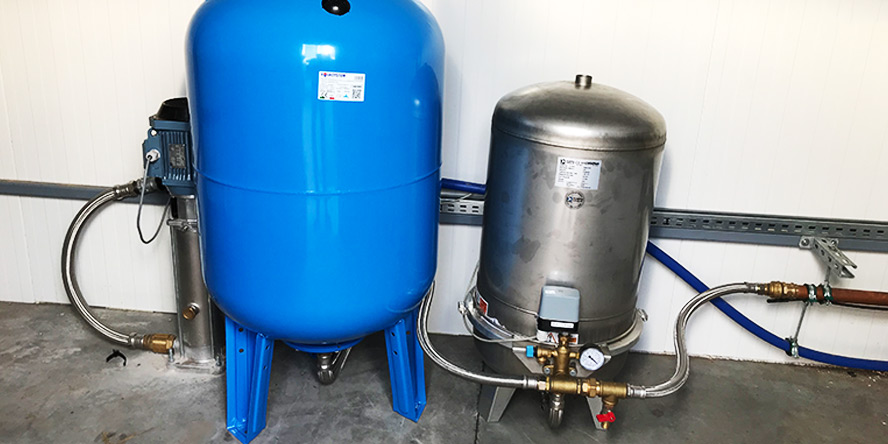
How to eliminate sparks from a sawdust pneumatic transport system
The spark detection and suppression system is mounted on ducts and transfers, used to transport the flammable product to equipment and instruments, and inside of which an explosion or fire may occur. Taking this into account, in the present case, the system sensors and extinguishing nozzles were installed at two points, i.e:
- on a 700 x 700 mm duct used for pneumatic transport of the sawdust to the cyclone after drying,
- on a DN400 duct, used to transport the dry sawdust from the cyclone to the silo.
In order to determine the installation points of the detectors and extinguishing nozzles on both ducts, their size and the amount of transported material per 1 m3 of duct volume were taken into account. In addition, the total response time of the system and the flow velocity of the material in the duct, which was previously measured, were also considered.
While in the case of the DN400 duct, we did not encounter any problems, in the case of the 700 x 700 mm duct, it turned out that it is too short in relation to its cross-section and airflow rate, which was about 30 m/s. With such parameters, the duct length should be at least 6-7 m. Unfortunately, it actually measured only 4 m. The plant had to undergo a conversion in order to extend the duct.
Installation of the hydraulic system under an unheated station roof
Due to the location of the drying installation and sawdust storage outside, under an unheated station roof, we provided a pipe heating installation with insulation casing and special thermal insulation covers for the extinguishing units. This ensures that all water supply pipers and the tank are protected against freezing over their entire length.